Background:
Corrosion:
It has now become a known fact that hundreds of thousands of coil failures have occurred during the last decade due to corrosion. The cause is most typically environmental pollutants, which range anywhere from salt-air, to household cleaning agents, pesticides, formaldehydes, building materials, and even off-gassing of food. Each of these contaminant sources can initiate corrosion in coil tubing in a year or less when the conditions are right.
Kinds of corrosion:
The two most common forms of coil corrosion are pitting and formicary. These two corrosive processes can occur in as little as a few weeks after installation. More typically, corrosion will begin appearing within a one to four-year period.
Choosing Corrosion Protection:
Choosing the most appropriate coil coating for the application could save the project thousands of dollars and eliminate repeat treatments. Choosing the wrong coil coating could reduce heat transfer capabilities and lead to higher energy bills
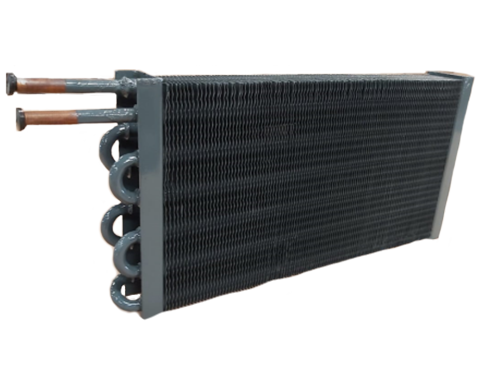
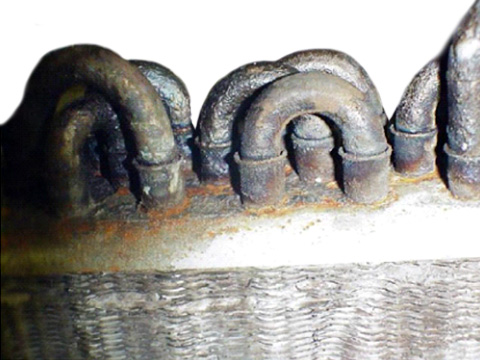
Description:
Water based self-etching epoxy resin-based coating is available in Grey colour, can be coated on all ferrous and nonferrous metals (as used in HVAC&R coil manufacturing) to give long term corrosion protection.
Types of I-Coat:
- Hydrophobic i-coat:
A permanent super hydrophobic surface improves condensation characteristics and allows for faster run off the condensate which improves heat transfer. It also reduces dirt and dust consolidation thereby reducing cleaning of the coil.
- Hydrophilic i-coat:
Due to hydrophilic surface the condensate on the aluminium fin will quickly spread and will not condense into water droplets, enables water droplets to flow off the surface without facing a lot of resistance to air flow.
Colour of i-coat: Grey
Advantages of “i – coat”:
- Corrosion Protection:
The entire surface of the coil is protected, including tubes, which remain free of corrosion allowing the coil to maintain its long-term heat exchange efficiency.
- Reduce Mould and Bacteria:
The coating contains permanent Ag+ technology (Ag+ = silver ion) reducing mould and bacteria growth within the coil. The coil stays clean and free of micro-biological contamination.
- Very Thin:
The coating is only 20 +/- 5 microns which does not affect heat exchange or air flow.
- Certification:
NSF Certification Standard to be used as a coating in and around food processing areas. NSF Registration Number 168020.
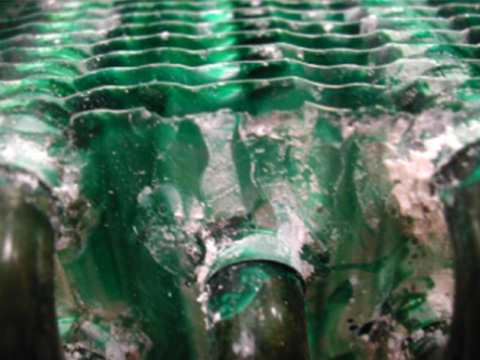
Technical Performance:
Corrosive Tests Results | ‘i- coat’ |
ASTM B117 Salt Spray, 3000 Hrs | Pass |
ASTM G85-A5, 2000 Hrs | Pass |
Features:
Features | i - coat |
---|---|
Water based | Yes |
Flammable | No |
Toxic | No |
Solvent additions | Water Only |
Clean up | Water |
Adhesion to coil components | Excellent/Self etching |
Thickness of deposited film | 20-25 microns |
Penetration of coil block | 100%Full immersion |
Penetration of fin collar/tube zones | Complete |